При его активном участии была разработана и внедрена уникальная в России установка для производства порошка из титана.
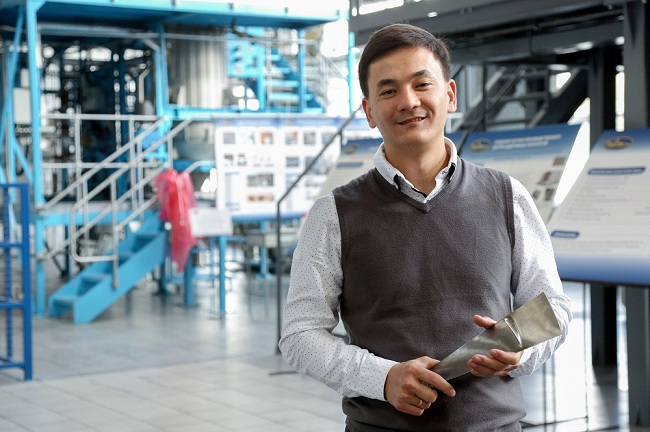
В 2011 году он окончил Московский институт стали и сплавов с красным дипломом. За время работы в институте назван лучшим работником ВИАМ (2015 год), а также отмечен благодарностью ГК «Роскосмос» за вклад в развитие отечественной космической отрасли.
- Максим Георгиевич, насколько важно для научно-исследовательского института собственное производство?
- Для ВИАМ, безусловно, очень важно. Задумки наших ученых и конструкторов прямо здесь, в институте, обретают реальные очертания. Можно сказать, перефразируя известную поговорку, что «все дороги» материалов, так или иначе, ведут в цех! Ведь именно здесь наши ученые могут впервые увидеть выплавку разработанного ими сплава, получить образцы, узнать о свойствах и понять – что получилось, верной ли дорогой идут.
В моем подчинении находится несколько цехов: это цех «Литье и жаропрочные сплавы», в котором также сосредоточено производство установок литейного оборудования и оборудования для нанесения покрытий (сложное оборудование для различных целей), «Цех нестандартных оборудований и изготовления образцов», цех «Кузнечно-прессовое производство», цех «Производство полимерных композиционных материалов».
Продукция наших цехов полностью востребована рынком. ВИАМ – разработчик практически всех основных сплавов, которые используются сейчас в авиации. Например, литая прутковая заготовка поставляется на все моторостроительные заводы России. Первый цех поставляет на заводы исходную шихту для литья. Штампованные диски, которые выдает четвертый цех, используются также в моторостроительный отрасли. Поэтому важность производства, очень плотно сотрудничающего с наукой, очевидна!
Хочу отметить, что качество изделий ВИАМ действительно широко известно. Многие производства не являются нашими конкурентами, в том числе и благодаря «научной форе», которая у нас есть. Установки и оборудование, которое мы производим, пользуются большим спросом. В том числе и потому, что мы предлагаем эксклюзивные разработки под нужды заказчиков.
- Заявки на изготовление оборудования – только от российских заказчиков?
- География сотрудничества ВИАМ как поставщика оборудования давно вышла за рамки Российской Федерации. Подобные установки УВНК мы поставили в Китай и Индию. Для коллег из Китая также изготавливаем установки для нанесения покрытий МАП. Одна из них уже передана заказчику и запланирован выезд туда наших специалистов для ввода установки в эксплуатацию.
- В вашем ведении находится стратегически важный участок ВИАМ. А с чего вы начинали?
- В 2011 году я окончил Московский институт стали и сплавов по специальности инженер-металлург и несколько месяцев проработал на заводе ООО «Втормет». Конечно, я не думал о такой стремительной карьере, а просто включился в профессию. Работал мастером в цехе по выплавке нержавеющей стали. Было жарко – особенно это чувствовалось летом. Открытая печь, открытый расплав. Температура сплава порядка 1600 градусов. Моей задачей было рассчитать шихту – там переплавляли цветной лом. По предварительному химанализу лома составлялась примерная «шихтовка» с расчетами: сколько какого лома нужно загрузить в печь, чтобы на выходе получить полуфабрикат заданного химического состава. Работа была сменная, а цех работал круглые сутки. Это был пробный экспериментальный цех, в котором на малых мощностях отрабатывали технологию, затем открыли большой производственный цех в Мценске, а здесь производство свернули.
- Вам пришлось искать новую работу?
- Да. Мой брат Павел Мин, который работает в ВИАМ с 2010 года, очень рекомендовал мне прийти именно сюда. Сам он занимается разработкой и выплавкой жаропрочных, в основном литейных сплавов, и кстати, недавно защитил кандидатскую диссертацию.
В 2012 году меня приняли в ВИАМ в качестве инженера-технолога первого цеха под начало нынешнего главного инженера ВИАМ, а тогда начальника производства Сергея Борисовича Трусова. Буквально через полгода он ушел на повышение и предложил мне курировать производство установок.
Как раз в это время ВИАМ заключил контракт на поставку двух установок для литья лопаток направленной кристаллизации УВНК 9А. Так, я стал и куратором этого проекта со стороны цеха. Мне пришлось глубже осваивать специальность, это было интересно и трудно одновременно. Проект мы завершили удачно. Как я упоминал выше – одну подобную установку в 2015 году мы собрали и по заказу индийских коллег. Еще одну сделали и для собственных нужд. Все эти работы велись параллельно. Далее были изготовлены также для ВИАМ ряд вакуумных индукционных и вакуумно-дуговая установки.
А по окончании этого масштабного процесса, который длился более четырех лет, в 2016 году меня назначили руководителем проектов. Именно в тот период я сосредоточился на производстве установок. Был заключен контракт с ПАО «Протон-ПМ» (предприятие ГК «Роскосмос») на поставку двух установок для литья фасонных отливок (на 80 и 200 кг). В конце 2017 года они были введены в эксплуатацию в Перми. Тогда же я был назначен начальником производства, получив персональную благодарность от Роскосмоса.
- Есть ли проекты, которыми вы гордитесь?
- В 2016 году совместно с конструкторским отделом нам удалось разработать уникальную, не имеющую аналогов в России, установку для получения металлических титановых порошков. Еще год ушел на отработку технологии на этой установке. Хочу особо отметить, что мы смогли исполнить бестигельное плавление металла: струя металла протекает через форсунку и разбивается металл газом, вот так красиво получается порошок. И сейчас ВИАМ может получать собственные титановые порошки. Раньше Россия покупала их за рубежом.
Установка была разработана конструкторским отделом ВИАМ, а мы на производстве занимались ее изготовлением. Но самое сложное – отработка технологии. Все было сделано силами небольшой группы в лице начальника конструкторского отдела ВИАМ Владимира Сергеевича Тартанова, заместителя начальника отдела главного технолога Глеба Сергеевича Киселева, плавильщика первого цеха Игоря Алексеевича Лосева и меня – под руководством главного инженера ВИАМ Сергея Борисовича Трусова.
Это была очень интересная работа! Но мы не останавливаемся на достигнутом и совершенствуем технологию.
- А как проходит ваш рабочий день?
- У меня очень динамичная работа. С утра обычно – производственное совещание со всеми руководителями цехов и отделов, на которых рассматривается план работ на грядущий день. Иногда возникает необходимость в каких-то мероприятиях, требующих оперативного решения. Два раза в неделю совещание у главного инженера. Раз в неделю я провожу совещание, посвященное производству установок. Все это запланированные основные мероприятия в обычном рабочем графике.
При этом всегда параллельно идет работа с обращениями заказчиков оборудования, поставкам продукции: переговоры, встречи, мозговые штурмы. У нас есть и основные партнеры, организации, которые специализируются на тех или иных видах производств, и у которых в нынешних рыночных условиях нам выгоднее заказать те или иные комплектующие. И уже мы их привлекаем для выполнения наших заказов. В общем, каждый рабочий день невероятно насыщен.
- А цеха приходится обходить?
- Обязательно. Стараюсь это делать ежедневно: ведь в мои обязанности входит проверка порядка и чистоты на производстве, рабочей дисциплины. Сразу скажу, что работники у нас дисциплинированные, соблюдают порядок и внутренние правила института.
- Много ли людей находится в вашем подчинении?
- Больше ста человек. Мы вместе занимаемся важным делом – развиваем науку, отечественное производство, все это происходит в тесном сотрудничестве.
Все наши рабочие – специалисты высокого класса, поэтому отдельно кого-то выделять я бы не стал. У нас все хорошо работают.
- С кем наиболее часто приходится контактировать?
- По производству оборудования, например литейных установок УВНК, мы плотно сотрудничаем с лабораторией «Технологии литейных процессов жаропрочных сплавов и сталей», они курируют технологию литья на этих установках, без них мы не можем сдать и ввести в эксплуатацию оборудование. В частности, Евгений Викторович Колядов занимается отработкой технологии по литью лопаток направленной кристаллизации. Технологию на установках по нанесению покрытий (это МАП) сопровождает лаборатория «Технологии поверхности и защитные покрытия для металлических материалов». В ВИАМ работает уважаемый профессор, доктор технических наук Сергей Артемович Мубояджян, с которым мы очень тесно сотрудничаем – он разработчик данных установок по нанесению покрытий, и конечно, без его консультаций мы не обходимся. По технологии изготовления порошка также плотно работаем с лабораторией «Порошковая металлургия и аддитивное производство». ВИАМ в прошлом году закупил печь с емкостью тигля 150 кг, на которой мы отрабатывали технологии получения порошка.
- Думаете ли вы о развитии цехов, как в дальнейшем представляете их работу?
- Направление развития нам задает руководство института. В зависимости от выбранной стратегии становится ясно, как необходимо переоснащать цеха. Например, сейчас на рынке растет потребность в порошке, и чтобы быть конкурентоспособными, необходимо увеличивать производство в этом направлении, потому что бурно развивается весь спектр аддитивных технологий.
- Что можно назвать профессиональным стимулом для вас?
- Мы занимаемся важным делом, развиваем отечественное производство. Оборудование, разработанное в ВИАМ, сравнивают с лучшими мировыми аналогами. Например, ПАО «Протон-ПМ» поставленные нами две установки планировали изначально приобрести у известной немецкой фирмы ALD, переговоры с которыми застопорились из-за санкций. Но мы успешно выполнили их заказ, кстати, выиграв конкурс и полностью выполнив их технические требования, получили очень благоприятные отзывы пермского завода: «оборудование мирового уровня, ничем не уступающее ALD».
Действительно интересно работать и развиваться вместе с талантливыми и трудолюбивыми коллегами – учеными, конструкторами, которым под силу разработать суперсложное и современное оборудование, и цеховиками, которые выполняют свою работу качественно.
- Остается ли время на досуг?
- Времени немного, но я стараюсь выбираться на фитнес. Люблю командные виды спорта и с удовольствием выезжаю с коллегами на базу отдыха ВИАМ в Конаково, где институт организует соревнования, в том числе по волейболу.
- У меня создалось впечатление, что вы везде стремитесь быть лучшим.
- Институт закончил с красным дипломом. Был отмечен как лучший работник ВИАМ в первом полугодии 2015 года. (Улыбается.)
- А что надо сделать, чтобы стать лучшим работником ВИАМ?
- В тот период я вел производство установок УВНК 9А. И служба главного инженера отметила мою работу, проголосовав за мою кандидатуру в конкурсе. Надо быть ответственным, считаю, стараться. Но делать это независимо от поощрений (которые, несомненно, греют душу), а во имя большого общего дела.
Интервью подготовила Светлана Офитова